在現代工業生產中,電機與泵類設備廣泛應用于各個領域,從能源電力到石油化工,從制造業到市政工程等。它們的穩定運行對于整個生產流程的順暢至關重要。而電機與泵類設備安裝過程中的一個關鍵環節便是軸對中,如果軸對中不準確,會引發一系列嚴重問題。例如,會導致設備振動加劇,使得軸承、密封件等關鍵部件磨損加快,不僅增加了設備的維護成本,還可能因突發故障導致生產中斷,給企業帶來巨大的經濟損失。據相關統計數據顯示,軸不對中是造成電機與泵類設備故障的主要原因之一,可導致電機能耗增加 15%-20% ,同時大大縮短設備的使用壽命。因此,精準的軸對中對于電機與泵類設備的高效、穩定運行意義重大,而愛司激光對中儀在這方面展現出的性能和應用價值。
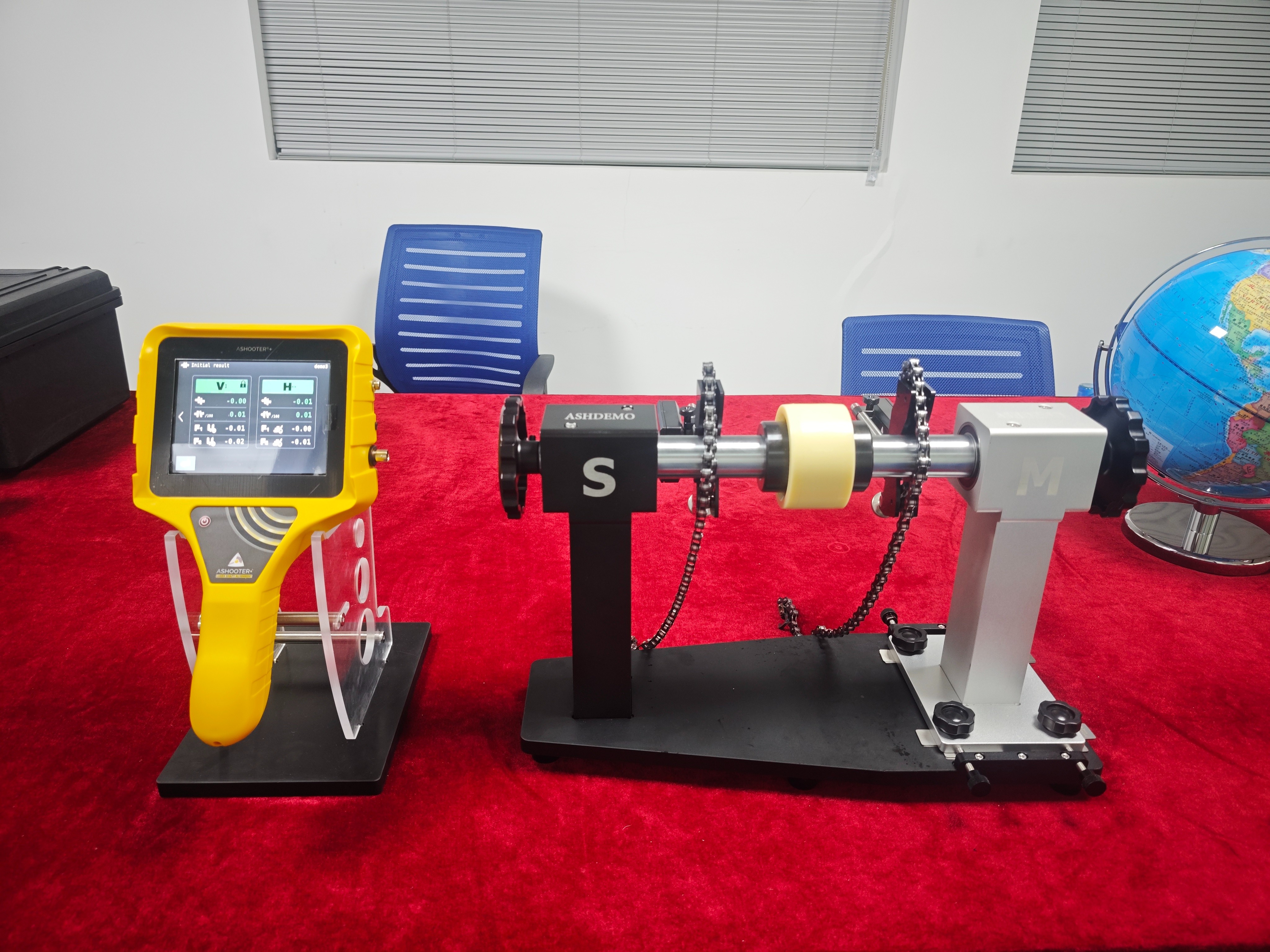
愛司激光對中儀之所以能夠在電機與泵類設備安裝中發揮關鍵作用,得益于其一系列先進的技術特性。
愛司激光對中儀采用了先進的激光傳感技術,以法國原廠的 ASHOOTER 系列產品為例,如 AS500 型號,其配備了 635 - 670nm 半導體激光發射器與 30mm 高分辨率 CCD 探測器。這種精密的組合使得對中精度達到了微米級,可精準識別聯軸器 0.1mm 以上的軸向偏移 ,能夠精確檢測軸系的徑向偏差(平行度)與軸向偏差(垂直度),相比傳統的百分表法,精度提升了 100 倍。在電機與泵類設備安裝中,如此高的精度能夠確保電機軸與泵軸精確對齊,減少因軸不對中產生的異常應力和振動,為設備的穩定運行奠定堅實基礎。

電機與泵類設備在運行過程中,由于內部能量轉換和機械摩擦等原因,會產生熱量導致設備部件熱膨脹。這種熱膨脹如果在安裝對中時未被充分考慮,設備在運行時軸系就會發生偏移,從而影響設備性能。愛司激光對中儀具備熱補償功能,在對中過程中,技術人員只需輸入設備運行時的預期溫度以及設備材料的膨脹系數等參數,儀器便能自動計算出因熱膨脹導致的軸系偏移量,并在冷態安裝時預留相應的調整值。例如,某高溫泵運行溫度為 80℃,通過愛司激光對中儀的熱補償功能計算后,在冷態調整時電機軸需預向下偏移一定量,從而確保設備在熱態運行時軸系偏差能控制在極小范圍內 ,有效避免了因熱膨脹引起的軸不對中問題。
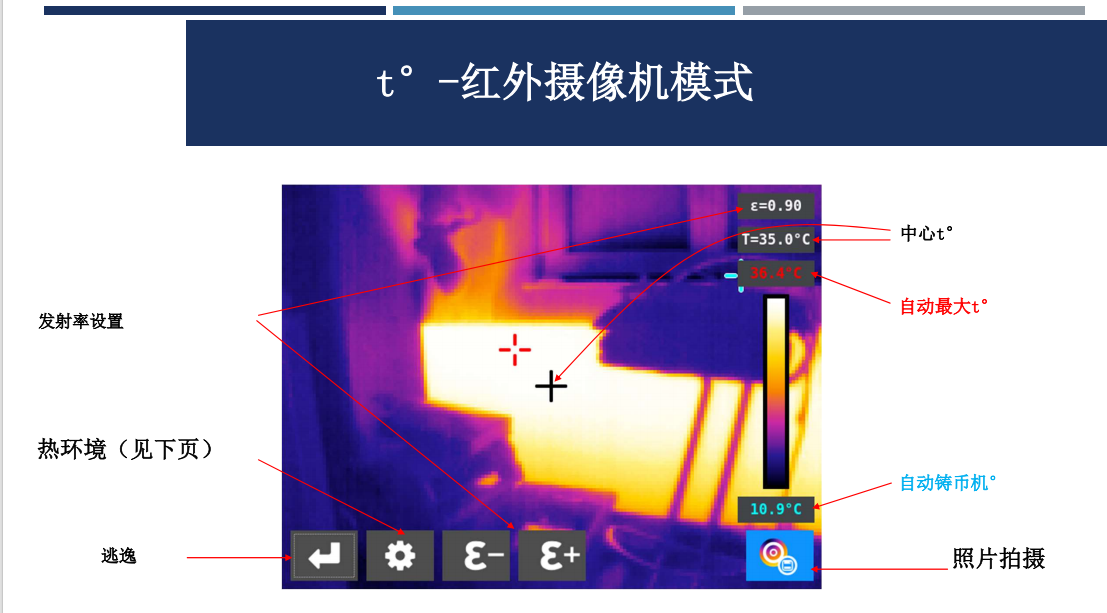
愛司部分型號的激光對中儀,如 AS500,創新性地將激光對中技術與紅外熱成像、振動頻譜分析技術深度集成。這種多技術融合的設計,使得儀器從單純的幾何精度檢測工具升級為設備健康狀態綜合評估系統。在電機與泵類設備安裝及后續運行監測中,紅外熱成像功能可實時監測設備表面溫度分布,穿透粉塵、油污等遮擋,及時發現因軸不對中導致的軸承摩擦發熱等內部過熱問題,例如能檢測到軸承因對中不良溫度異常升高至 95℃(正常工作溫度應≤65℃) ;振動頻譜分析功能則通過傅里葉變換(FFT)分解振動信號,識別出不平衡、不對中、軸承磨損等故障特征頻率,如能捕捉到軸承外圈故障頻譜出現的特定邊帶頻率峰值 。通過這三種技術的數據相互印證,可構建完整的故障鏈,全面準確地判斷設備的運行狀態,為電機與泵類設備安裝調試及故障排查提供有力支持。
在使用愛司激光對中儀進行電機與泵類設備安裝對中前,技術人員需要做好充分準備工作。首先,要仔細檢查設備的外觀,確保電機和泵體無明顯損壞、變形等情況。然后,清理設備的安裝基座,保證基座表面平整、清潔,無雜物和油污,為后續設備的安裝和對中提供良好的基礎。接下來,選擇合適的愛司激光對中儀型號及相應配件,如針對不同軸徑選擇適配的磁性安裝支架、延長桿等。以 AS500 激光對中儀為例,將其激光發射模塊(M 端)和接收模塊(S 端)分別安裝在電機軸和泵軸上時,需使用磁性支架確保支架與軸體貼合緊密,間隙要小于規定值,同時利用儀器內置的數字傾角儀校準支架水平,使氣泡偏差≤規定角度 ,保證儀器安裝的準確性。
安裝好愛司激光對中儀后,即可開始對中測量。啟動儀器,選擇合適的測量模式,如雙激光束模式等。技術人員手動盤動電機軸和泵軸,使軸分別處于 0°、90°、180°、270° 等不同位置,在每個位置上,愛司激光對中儀會實時采集并記錄軸系的徑向偏差(ΔR)與角度偏差(Δθ)數據,測量精度可達 ± 規定精度值 。例如在某電機與泵安裝對中項目中,測量得到垂直方向的徑向偏差 ΔRv = + 規定數值(表示上偏),水平方向的徑向偏差 ΔRh = 規定數值(表示左偏),角度偏差 Δθ = 規定數值(表示上張口) 。這些精確的數據為后續的設備調整提供了準確依據。同時,若設備運行時存在熱膨脹情況,在測量過程中可啟用儀器的熱膨脹補償功能,輸入設備運行溫度、材料膨脹系數等關鍵參數,儀器自動計算出冷態預留值,以確保設備在熱態運行時軸系的良好對中狀態。
根據愛司激光對中儀測量得到的數據,技術人員對電機與泵類設備進行相應調整。如果徑向偏差或角度偏差超出允許范圍,可通過調整設備的安裝位置,如在設備基座下增減墊片等方式來糾正偏差。在調整過程中,持續觀察激光對中儀的實時數據反饋,直至軸系的徑向偏差和角度偏差達到設備安裝要求的精度范圍內。例如,某電機與泵安裝時,初始測量發現電機軸相對泵軸存在一定角度偏差,通過在電機基座底部一側增加合適厚度的墊片,并利用激光對中儀實時監測調整效果,最終使角度偏差滿足了設備運行的精度要求。對于一些復雜的設備安裝場景,如大型電機與多級泵的對中,可能需要多次反復調整和測量,愛司激光對中儀憑借其高精度的測量和直觀的數據顯示,能夠幫助技術人員高效、準確地完成設備的調整與校準工作。
通過使用愛司激光對中儀對電機與泵類設備進行精準對中安裝,設備的運行穩定性得到了極大提升。軸系的精確對齊減少了設備運行時的振動和異常應力,使得軸承、密封件等關鍵部件的工作環境得到改善,磨損速度明顯減緩。以實際案例來看,眾多采用愛司激光對中儀對中的電機與泵類設備,運行過程中的振動有效值普遍從較高水平大幅降低,如從 12mm/s 降至 4mm/s 左右 ,設備運行更加平穩,大大降低了設備因振動等問題引發故障的風險,保障了設備的長期穩定運行。
由于設備運行穩定性提高,電機與泵類設備的維護成本顯著降低。一方面,關鍵部件磨損減緩,延長了軸承、密封件等零部件的更換周期,減少了零部件采購成本。另一方面,設備故障頻率降低,減少了因設備停機維修所帶來的人工成本、生產停滯損失等間接成本。例如,某企業在使用愛司激光對中儀后,電機與泵類設備的維修次數大幅減少,年度維護成本降低了 40% 以上 ,為企業節約了大量資金。
精準的軸對中使得電機與泵類設備能夠以最佳狀態運行,提高了設備的工作效率。例如,泵類設備的流量和揚程更加穩定,能夠更高效地輸送液體介質,電機的能耗也因軸對中準確而降低,避免了因軸不對中導致的額外能量損耗。在生產過程中,設備穩定高效運行減少了因設備故障導致的生產中斷時間,保證了生產流程的連續性,從而提升了整體生產效率。據統計,在使用愛司激光對中儀優化電機與泵類設備安裝后,相關生產環節的生產效率提升了 20% - 30% 不等 ,為企業創造了更多的經濟效益。